Posted in Minoli
4th April 2022
We’ve all read the commentary in mainstream and industry press about constricted supply and increases in building material costs.
We know first-hand, and from talking to our clients and reseller partners, the difficulties these trading conditions pose, and so wanted to set out the actions we’re taking to manage and mitigate the impact, as best we can.
Not only have we seen a global post-pandemic surge in demand for construction materials, but we here in the UK have also had the added complexities of the Brexit transition.
Now, with gas and clay being fairly essential ingredients in porcelain tile manufacturing, and the production plants sourcing much of the raw material from or through Ukraine (especially for the XL formats), the terrible conflict in that region is further impacting supply and in turn pricing.
This ‘perfect storm’ of circumstances causes difficulties for all suppliers of porcelain-based tile products and of course those operating in the broader construction sector, but we at Minoli are perhaps in a better position than some.
Firstly, as our existing clients and partners will know, our business model is based on holding vast quantities of stock here in the UK– upwards of £3.5m in net cost value – at our warehouses and distribution centre in Oxford. This means that we can generally ‘iron out’ the peaks and troughs in production supply and offer a stable delivery proposition to our clients.
We also run our own fleet of trucks and drivers, so we have greater control over our delivery mechanism, we can plan our own routing and also prioritise deliveries to the most urgent cases of demand.
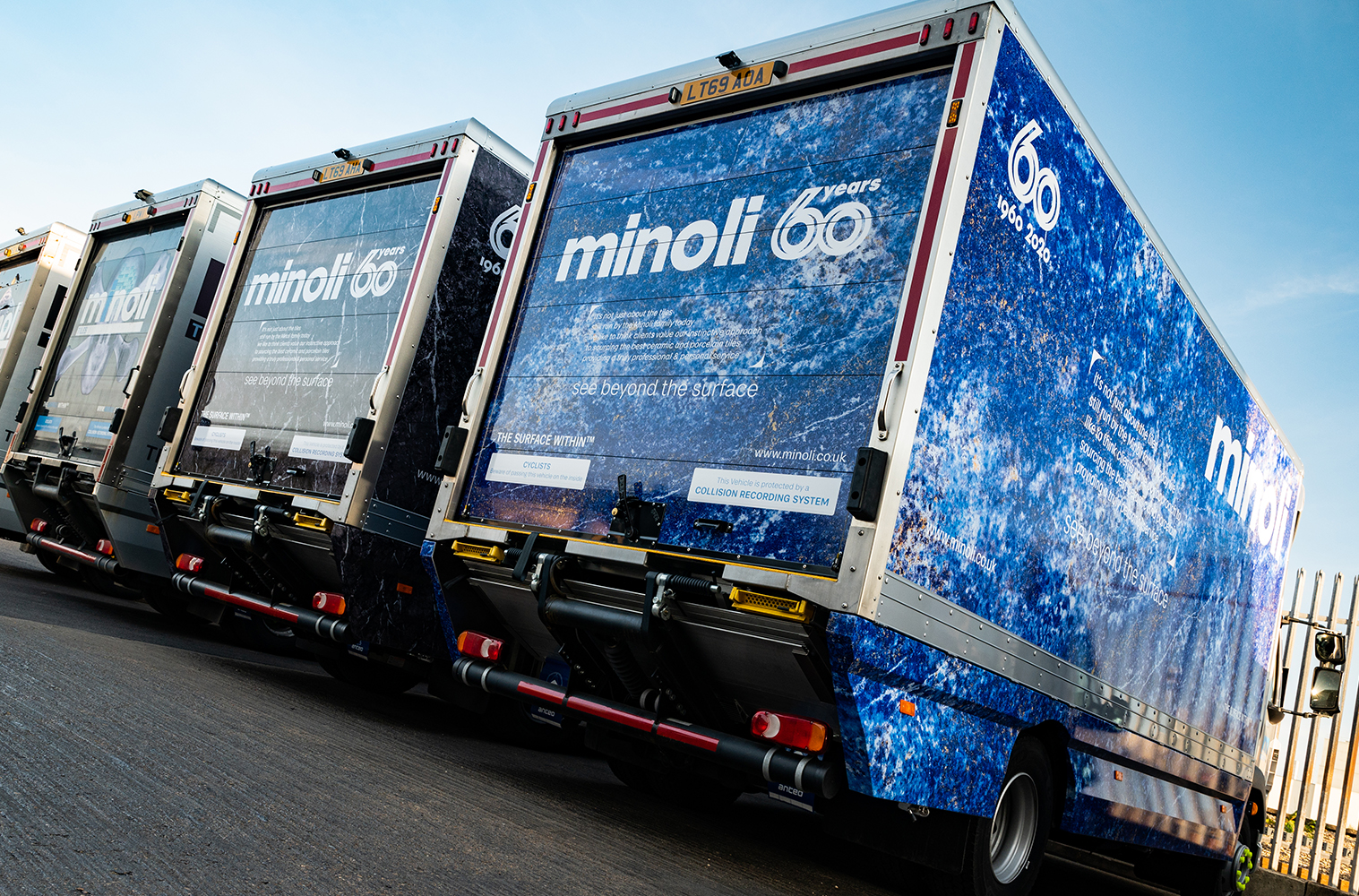
Established in 1960, we have some on the longest-standing supply chain relationships in the industry. Minoli only source products from the leading, topflight production plants in Italy and Spain. Unlike some second-tier factories who are having to cease production, our main production partners have raw material reserves, are quickly establishing new supply lines and are in fact actually ramping up production to meet demand, which really has not declined at all post lock-down.
Having acquired the sites adjacent to our HQ in recent years, we can accommodate a greater stockholding and have pre-ordered in excess of 50 containers of our most frequently specified lines, over and above the normal stock holding. In preparation for its arrival, an additional covered storage facility has been acquired to accommodate our clients’ medium-term needs.
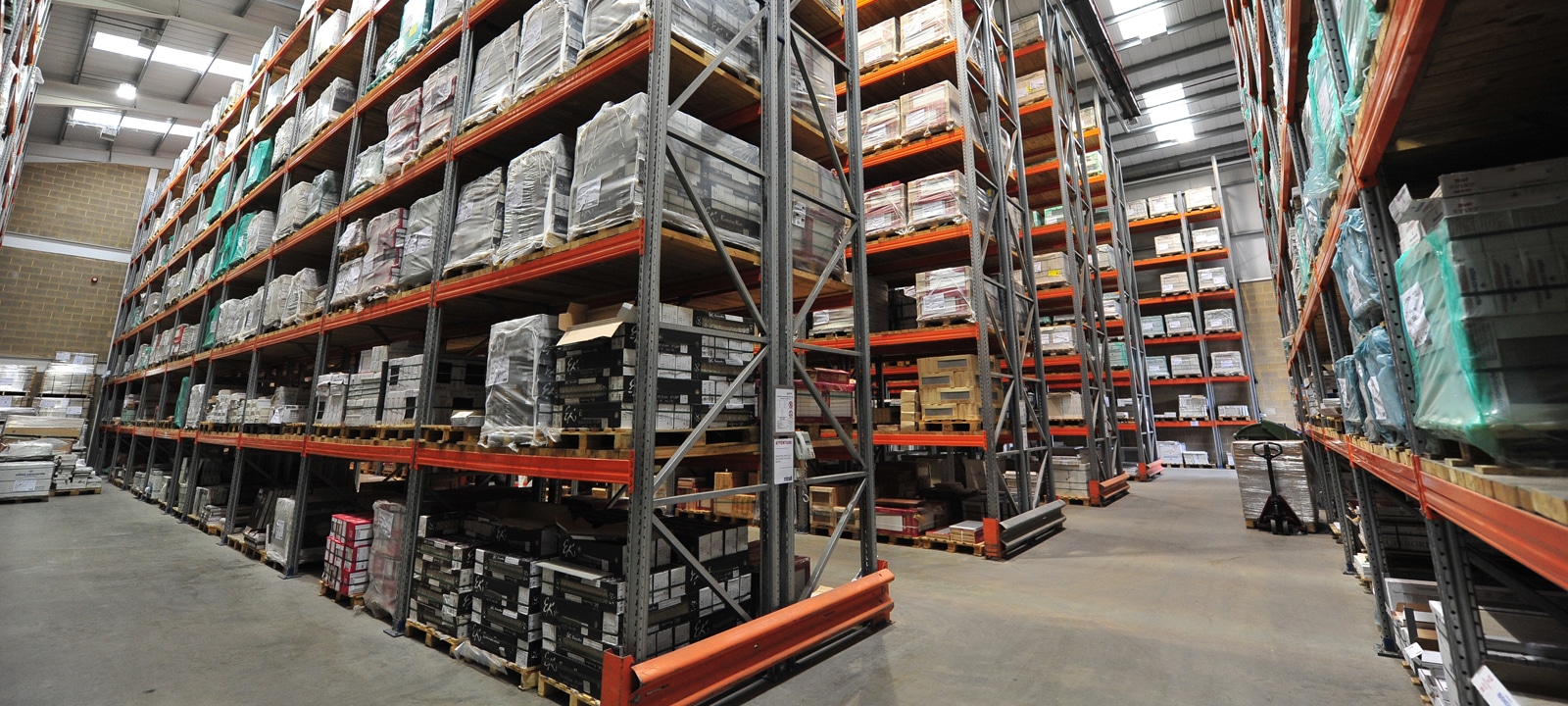
Lastly, with regard to material and transport, rather than apply a blanket increase to recognise these unavoidable cost changes, as some in our sector have done, we have reviewed line by line and reset our entire product portfolio price list with the bare minimum viable adjustments applied.
All of this underlines our ongoing commitment to offering our clients outstanding value and levels of service considered second to none. And whilst the above has taken great efforts by our team in almost all departments, we hope that our customers and distribution partners will be able to enjoy the reassurance of business as usual from Minoli.